What Are the Top 5 OSHA Violations and Their Relevance to Loading Docks
Loading docks are bustling work environments that present numerous and serious safety risks and hazards. Ensuring a safe and compliant workplace is crucial in preventing accidents, injuries, and costly OSHA violations. In this blog post, we will discuss the top 5 OSHA violations and their relevance to loading docks, exploring strategies for prevention and the consequences of non-compliance.
-
This article provides an overview of the top 5 OSHA violations in loading docks and outlines strategies for their prevention.
-
Consequences of non-compliance with OSHA regulations include financial penalties, safety risks, and reputational damage.
-
Employers should prioritize employee training, safety audits/inspections & implementing safety systems to prevent OSHA violations & maintain a safe working environment.
Top 5 OSHA Violations in Loading Docks
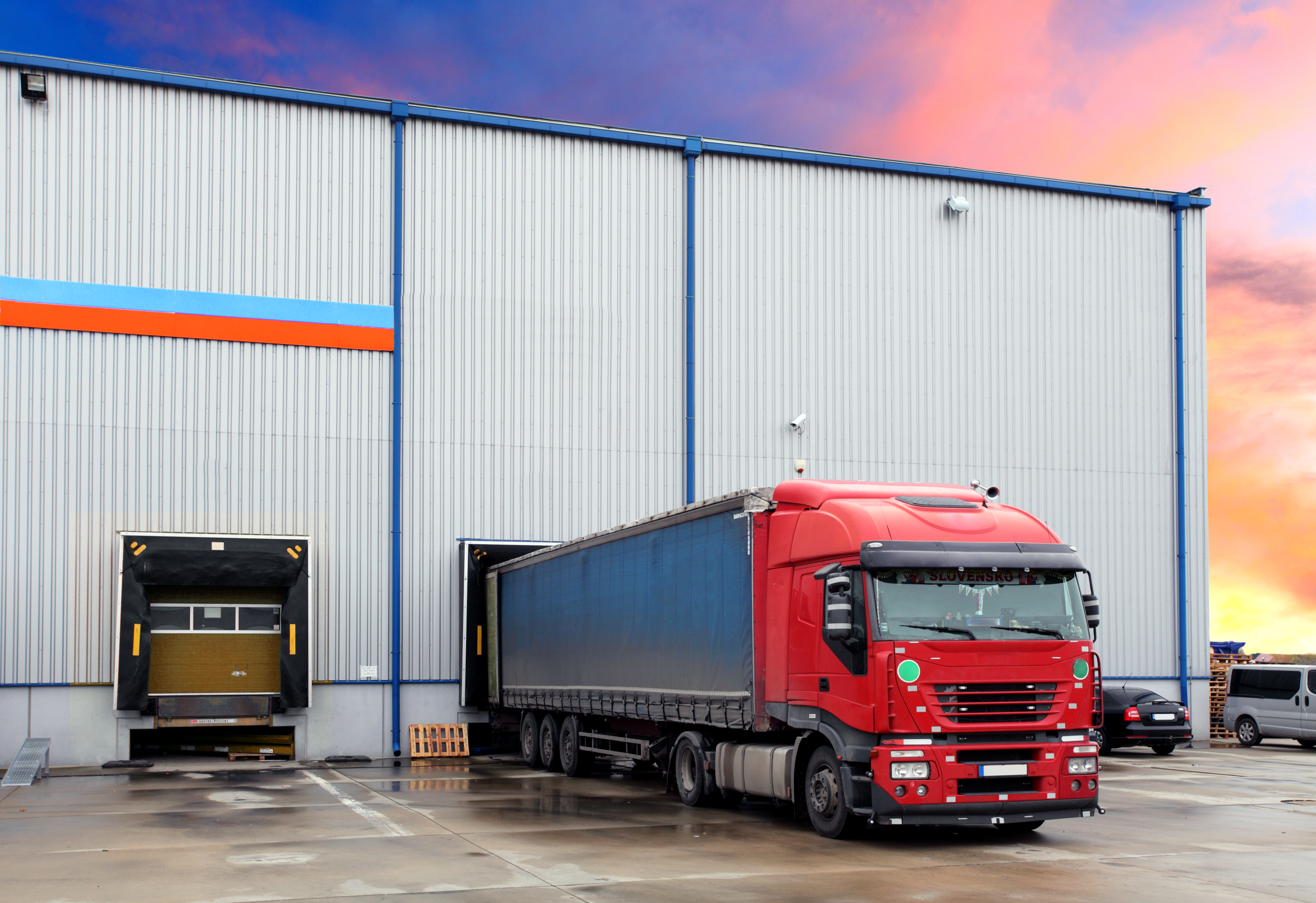
Adhering to OSHA standards is essential in protecting workers from potential hazards found in loading docks, as failure to do so can incur workplace injuries or even fatalities, as well as costly fines and penalties. This blog post explores the five highest-ranking violations of these safety regulations - fall protection, hazard communication, powered industrial trucks (PITs), personal protective equipment (PPE) and lockout/tagout procedures, with an emphasis on employers devising effective strategies for their prevention.
For one thing, PITs must be operated by well-trained personnel who have been given a comprehensive overview of safe operations guidelines. This includes adhering to all relevant rules or prohibitions set out at each site they work at. Specific PPE should always be supplied when working around potential dangers such as hazardous substances or chemical gases that could cause harm if exposed directly without adequate safeguards put into place.
It’s also important for business owners and managers alike to become familiar with lockouts tagouts requirements since unprotected machinery poses significant risks – both machines themselves need securing before any maintenance tasks are carried out while power sources need to be switched off until everything has been checked over completely before resuming use again. Safety systems will help create safer conditions which will minimize overall risk levels over time more efficiently than just relying solely on enforcement upon adherence only.
Fall Protection
The construction industry requires adequate fall protection in loading docks to ensure worker safety and protect against OSHA violations. Fall risks can come from different sources such as unstable dock edges, wet surfaces, or lack of guardrails surrounding elevated workstations. According to the Centers for Disease Control and Prevention (CDC), one-third of all deaths related to construction are a result of a fatal fall accident - making it essential that employers prioritize implementing protective measures like railings, nets, training sessions etc., among other factors outlined by Standard 1926.503 issued by OSHA which mandates staff education on fall hazards and how best recognize potential threats in order to minimize their likelihood of occuring.
Hazard Communication
It is necessary for employers to carry out effective hazard communication in loading docks, especially due to the potential risks associated with hazardous materials. OSHA requires comprehensive programs so that staff are aware of any dangers and can handle these substances safely. This includes informing workers about workplace hazards, offering training programmes that help them comprehend chemical identities, and providing safety data sheets along with labels on dangerous items. Failure to comply may lead to endangering employee's wellbeing which will result in violations from OSHA. Health administration has an important role here to help managers create protective initiatives including employee seminars and focusing on appropriate protection measures regarding worker safety. Doing so avoids charges against their company issued by authorities like OSHA who take precautionary rules seriously when it comes to defending personnel’s lives and wellbeing while at work.
Powered Industrial Trucks
Powered industrial trucks, such as forklifts, are a common sight in loading docks and can be the root of OSHA infractions if not managed appropriately or operated correctly. Complications may arise from using hazardous vehicles, lack of proper training on regulations enforced by OSHA regarding powered industrial truck usage, or failing to comply with these guidelines.
Employers must take measures to guarantee safe operation and qualified instruction when handling this machinery so that they do not face citations for breaching Occupational Safety & Health Administration laws associated with powered industrial units. Routine checkups should occur along with inspections which target problems that could lead to mishaps or charges being made against an employer violating OSHA laws in connection to powered industrial trucks.
Through prioritizing workplace safety, employers have the ability to limit potential OSHA penalties related specifically to loading dock operations.
Personal Protective Equipment (PPE)
Employers are obligated to follow OSHA standards by supplying construction workers with personal protective equipment (PPE) such as eye and face protection, respirators, and clothing suitable for the loading dock. Failing to do so can lead to hazardous conditions with possible serious injuries or hefty fines from OSHA violations. To prevent any potential problems, employers must put into action an effective PPE program while also training workers on its use, maintenance, and storage processes that comply with OSHA regulations.
Lockout/Tagout Procedures
Lockout/tagout measures are imperative at loading docks to shield workers from harm that could be caused by sudden release of hazardous energy during servicing. OSHA mandates businesses to have a lockout/tagout process in place to protect personnel against the danger posed by electricity, hydraulic, pneumatic and mechanical sources. Disregarding these stipulations can lead to fines being leveled on employers. Consequently it is up to bosses to ensure thorough implementation and enforcement of such programs, appropriate training, and creating an atmosphere secure enough whereupon adhering strictly towards upholding OSHA guidelines becomes second nature ensuring utmost worker protection.
Strategies for Preventing OSHA Violations in Loading Docks
Loading dock safety is paramount in order to comply with OSHA regulations and avoid costly penalties, so employers should implement certain preventive strategies such as employee training, regular safety inspections and audits, plus implementing appropriate security systems. These practices will help reduce the risks of workplace accidents or injuries while also ensuring compliance with relevant laws. Understanding potential hazards associated with loading docks, along with these five main OSHA violations, can aid managers in maintaining a safe working environment for their employees. Employees have the right to a safe work environment every time they show up on duty, day or night, 24x7 no questions asked!
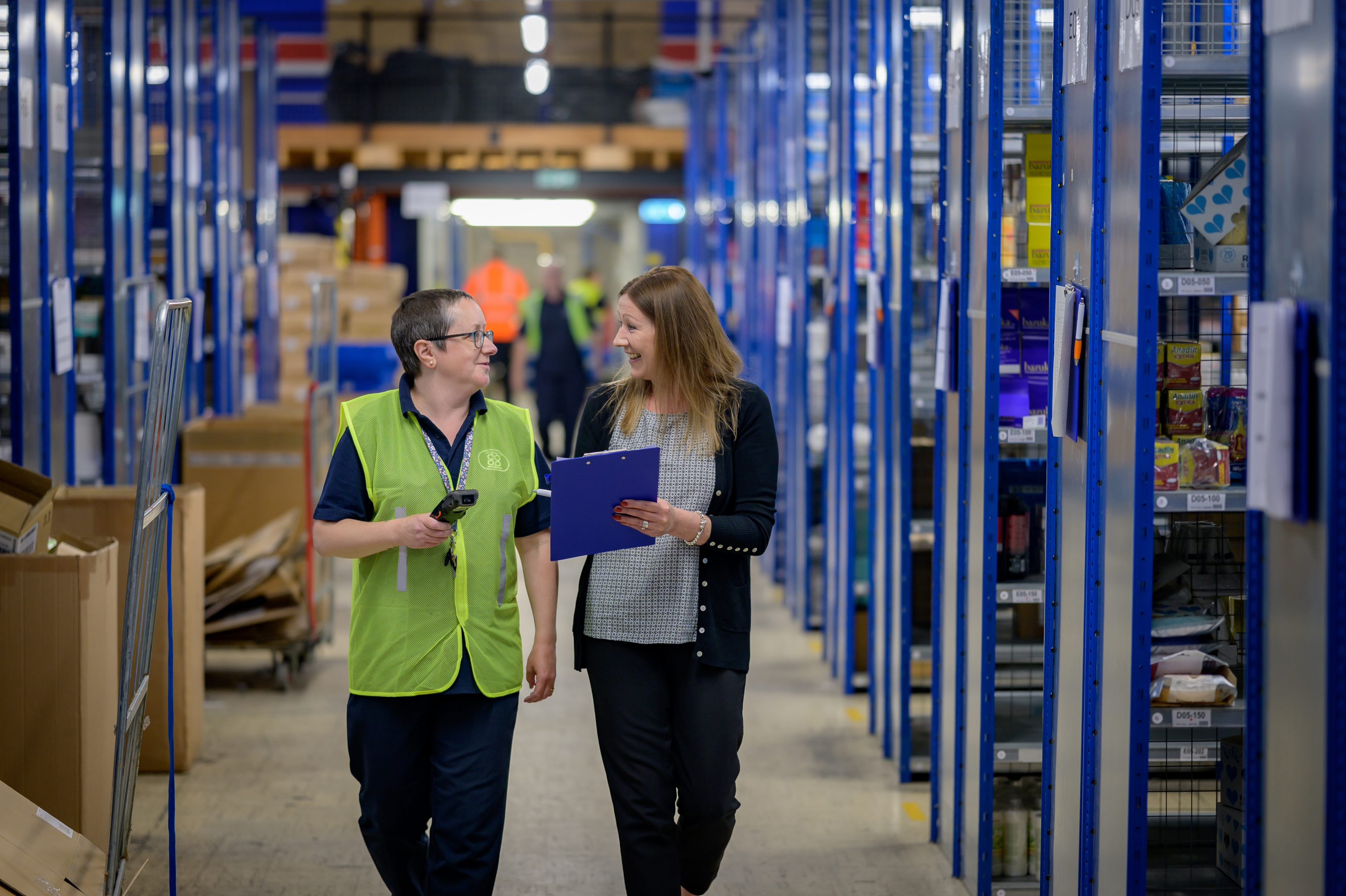
Employee Training
Employers are encouraged to provide comprehensive occupational safety training for their employees in order to prevent OSHA violations and create a secure working environment at loading docks. Training should include topics such as recognizing hazards, using PPE correctly, dealing with hazardous materials, and operating powered industrial trucks safely. It is important that refresher courses be conducted regularly so workers stay up-to-date on the latest safety guidelines and regulations set by OSHA. By meeting these training requirements, as well as providing appropriate instruction about safe practices, organizations can minimize the risk of injuries while increasing productivity levels at loading docks.
Regular Safety Audits and Inspections
Performing safety audits and inspections on a regular basis can assist employers in detecting any potential hazards that could lead to OSHA violations. This should cover all aspects of loading dock operations, including hazard communication, fall protection procedures, the maintenance of powered industrial trucks (PITs), as well as dock safety procedures, such as lockout/tagout protocols.
Through such assessments, workplaces are able to address issues before accidents occur or penalties need to be paid out, making it crucial for ensuring compliance with existing OHSA regulations whilst also creating safe environments for employees. By continually evaluating and strengthening safety measures at dockside locations across industries, organisations gain more control over avoiding accidents from happening in the first place.
Implementing Safety Systems
In order to better protect workers from potential hazards and ensure OSHA compliance, the use of safety systems in loading docks is encouraged. These include fall protection measures such as guardrails and safety barriers, hazard communication programs for chemical handling, lockout/tagout procedures that control the control of hazardous energy and sources. By implementing these methods employers can create a safe environment while also avoiding any type of OSHA violations. It emphasizes the importance of taking necessary steps towards preventing injury on-site.
The Consequences of OSHA Violations in Loading Docks
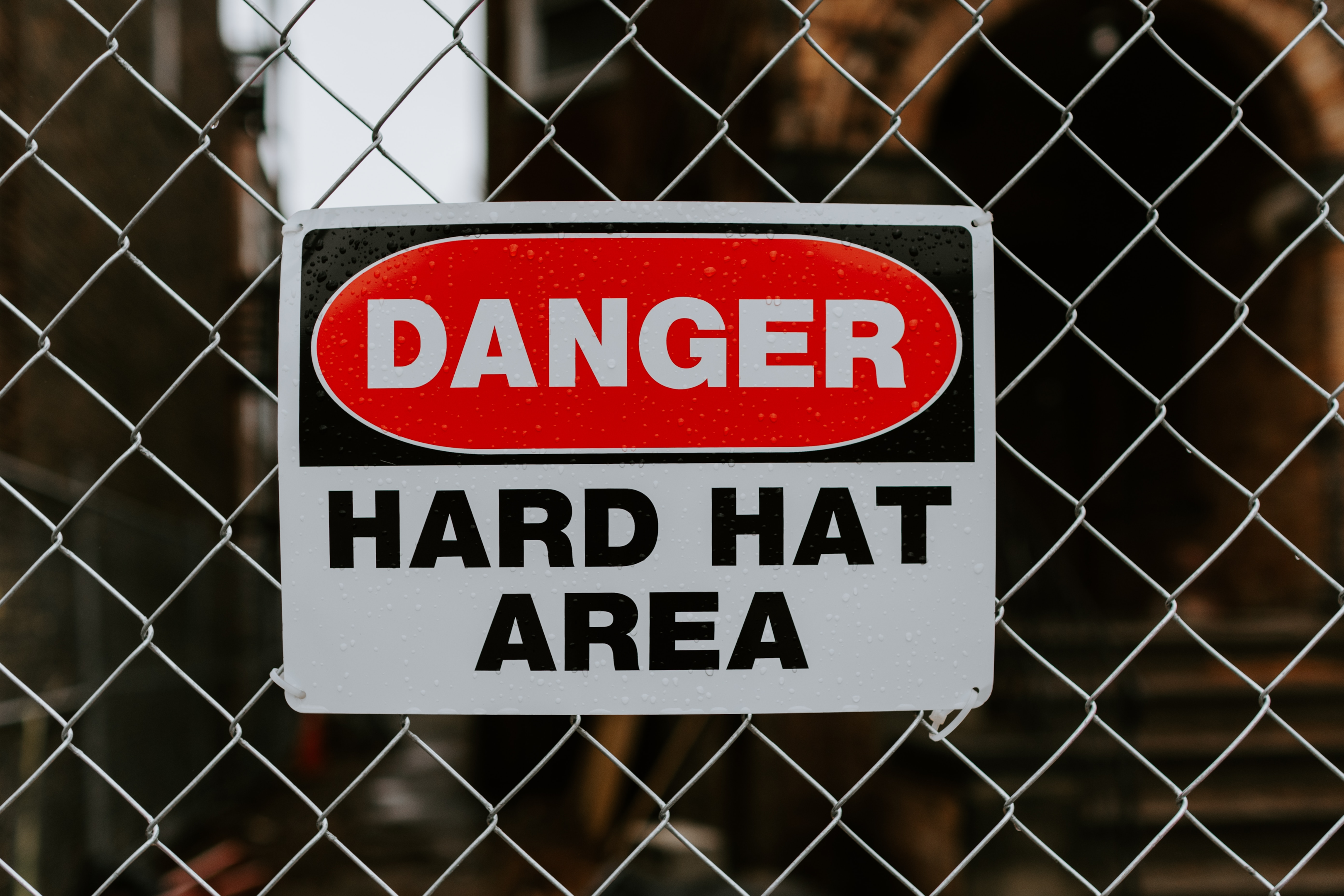
The ramifications of violating OSHA regulations in loading docks can be severe, from hefty fines to putting worker safety at risk and damaging one’s reputation. This emphasizes the need for strict adherence to these rules as well as establishing proper security protocols in loading dock safety procedures areas.
In this part, we will go into greater depth about each consequence mentioned above.
OSHA Penalties and Fines
Neglecting to comply with OSHA regulations and address citations can lead to serious fines, ranging from $13,260 per violation up to a maximum of $132,598. As such, businesses must put safety first when it comes to their loading docks in order to avoid these hefty financial penalties. Ensuring compliance with relevant guidelines as well as implementing the necessary safety measures is essential for employers wishing to avoid any costly punishments that come hand-in-hand with serious violations of OSHA rules.
Impact on Worker Safety
It is imperative for employers to comply with OSHA regulations in order to protect their workers and minimize healthcare costs. Implementing effective safety measures like employee training, regular safety audits, and installing appropriate systems, are key components of providing a safe working environment within loading docks so that there will be less risk of OSHA regulation violations occurring which could potentially lead to injury or even death. Worker safety should remain the priority throughout this process as it can help prevent unfortunate outcomes associated with OSHA violation consequences.
Reputational Damage
The consequences of failing to adhere to OSHA regulations can be far-reaching, as not only are there potential penalties involved, but it also puts the business' reputation and customer trust at risk of negative impact. Companies must take active measures towards ensuring workplace safety if they wish to mitigate the risks associated with violating these standards - this way, employers will show their commitment for compliance and reduce the chances that an OSHA violation taints its image or harms business opportunities. Such efforts would include avoiding any risky scenarios when possible, as well as addressing violations quickly, so it does not adversely affect worker safety.
Case Studies: Loading Dock OSHA Violations and Solutions
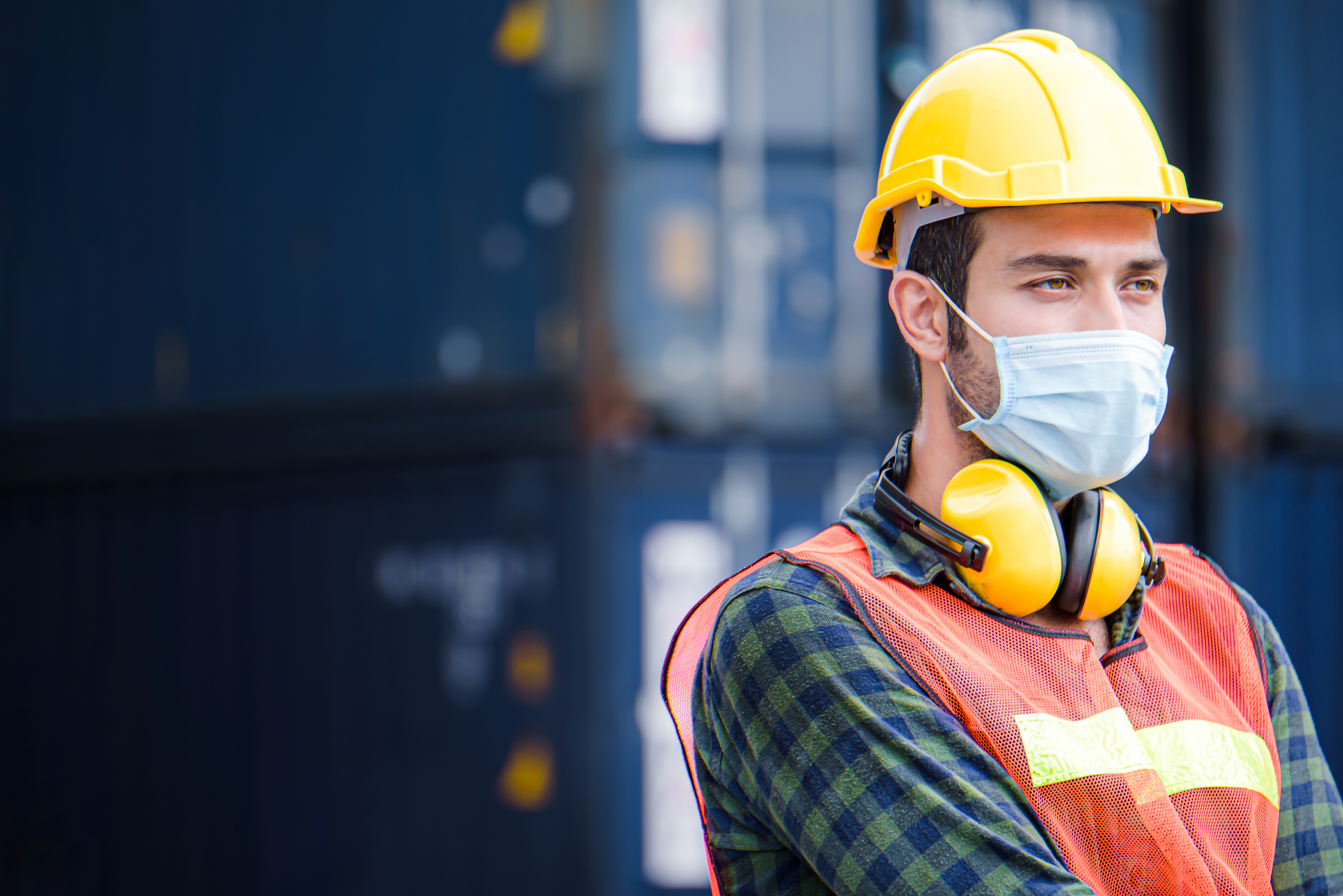
To demonstrate the importance of resolving OSHA violations in loading docks, we will analyze two examples that illustrate both the repercussions of disregarding these regulations and what is necessary to correct them.
Example 1: Fall Protection Violation
An accident at the loading dock resulted in a worker being severely injured after falling from an unprotected edge. Subsequently, this facility was subject to costly fines and legal proceedings due to their neglect of proper fall protection systems. To prevent such dangerous incidents from occurring again, they implemented guardrails as well as other safety barriers along with training for all employees regarding proper fall protection measures so that both OSHA standards were met and overall employee safety was improved.
Example 2: Hazard Communication Failure
The chemical storage facility had a communication breach, resulting in personnel not being informed of the risks related to the chemicals they were dealing with. This resulted in an accident and necessitated evacuation of the site. To rectify this OSHA violation and increase overall safety levels at their loading dock, they implemented a comprehensive hazard communication program, including providing employees with relevant safety data sheets along with suitable labelling on hazardous substances as well as regular training for staff members.
Summary
Prioritizing safety and compliance in loading docks is essential for preventing the most frequent OSHA violations, shielding a company’s credibility as well as their economic stability. To ensure compliance with workplace regulations, employers should put into practice effective solutions like regular staff instruction sessions, combined with audits and inspections, that would detect potential hazards early on before they become major issues. By investing in training programs plus precautionary technologies, such as efficient safety systems, companies can guarantee that their working environment meets all of the necessary requirements established by OSHA’s protocol.
Frequently Asked Questions
What are the 5 most frequent OSHA violations?
In 2022, OSHA violations that were the most frequent included fall protection, hazard communication, lockout/tagout and respiratory protection with scaffolding being in fifth place. These particular areas of concern demonstrate an ongoing need for safety management within workplaces.
What are major OSHA violations?
OSHA violations encompass any failure to properly address known dangers in the workplace which could cause severe harm or fatality.
What are the top 5 OSHA violations in loading docks?
OSHA violations are commonly seen around loading docks, and the top 5 safety concerns include: fall protection training, hazard communication protocols, utilization of powered industrial trucks with personal protective equipment in use when necessary and proper lockout/tagout procedures followed. It is important to uphold these measures for a secure environment for all who work at or near loading dock areas.
Owner, Parts Brite
My background is in Electrical and Software Engineering, but since I started PartsBrite.com in 2016, I've focused on everything related to docks.
My team and I are here to help those looking to repair or replace their dock levelers, bumpers, door, and door lights.
1-855-PartsBrite | partsbrite.com | paul@partsbrite.com
Leave a comment